Whew, 5 months since my last update!
Needless to say, there has been A LOT going on in my life. Too much for details. Other things needed more attention than the Bronco. Summer came and went before I knew what happened. Things are getting back to normal and the push on the Bronco has resumed.
Going back to early May, I ordered a clutch for the R2.8. Nothing special, just another McLeod like the unit I had before. I could have re-used the old one, but it was grooved and I wanted fresh parts. Well that started another fiasco similar to the intake manifold problem I had last summer that started this whole engine swap. I was getting a pit in my stomach at the prospect of waiting months for back ordered parts. I was able to track down a different clutch kit and order it. Well it showed up and it was definitely not designed for a hydraulic throw out bearing. So I jumped brands and bought a Luk clutch kit that seems like it will fit the build. Nothing fancy, just a standard clutch with a little extra holding power.
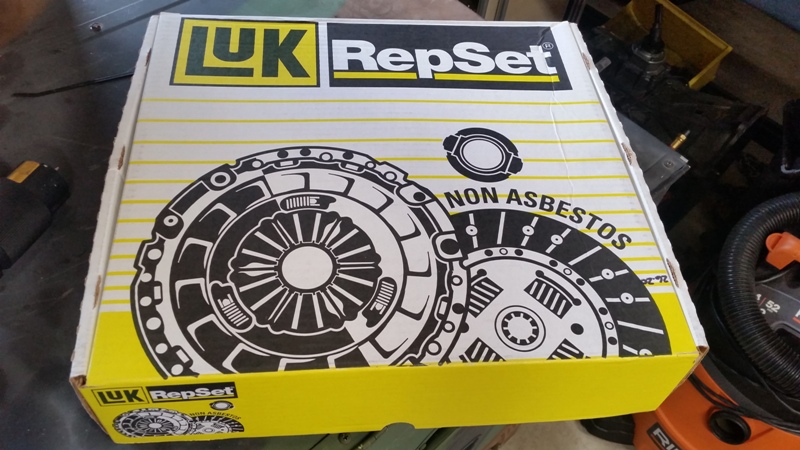
Laying all three clutches side-by-side, you could see the difference in the spring fingers. The new McLeod clutch fingers did not extend as far towards the crank centerline and the hydraulic throwout bearing wanted to pass right through. Additionally, the distance from pressure plate to top of clutch fingers was slightly different.
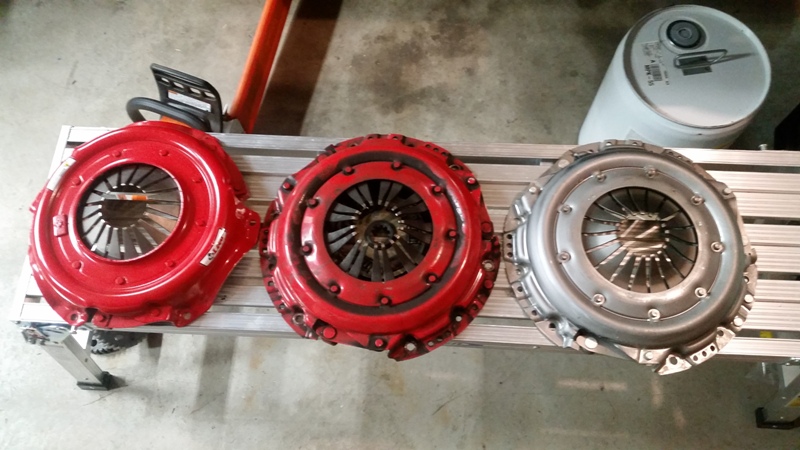
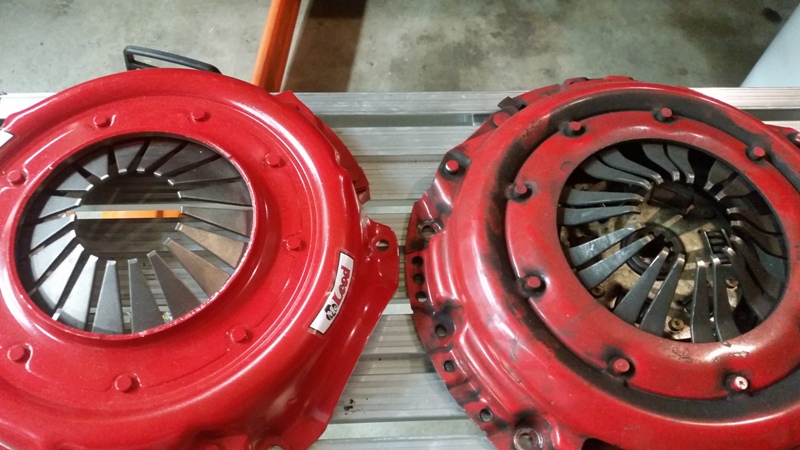
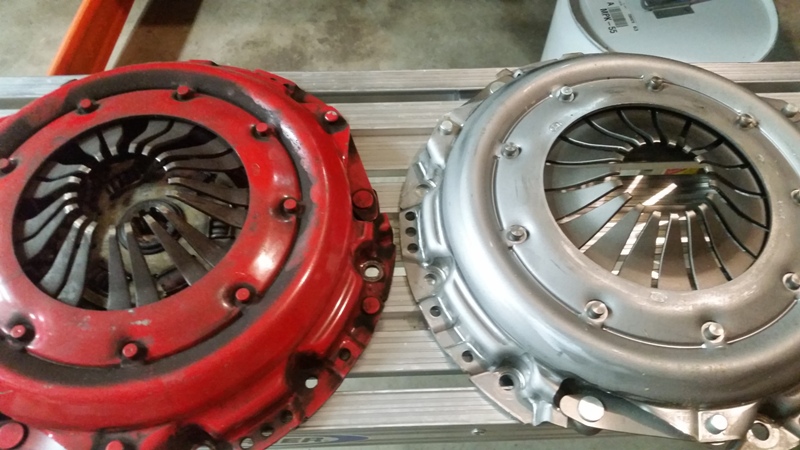
Ironically, all three pressure plates were stamped "Luk".
With new clutch in hand, about mid-June, I dis-assembled the adapter set and fit the clutch.
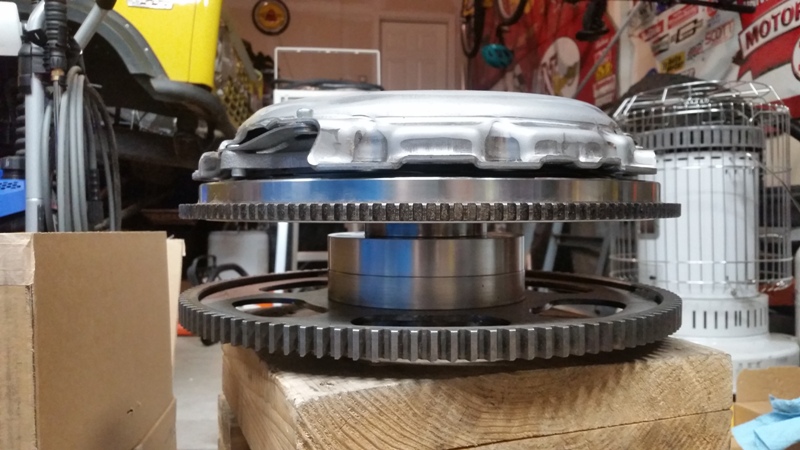
The stack of parts is pretty tall, not ideal, but it should work fine. Weight-wise, its heavy. Both the stock Ford 351 flywheel and the Cummins flywheel hover around 25lbs. The stack with adapters is pushing 45lbs. However, the majority of that weight is much closer to the crank centerline, so additional rotational inertia is minimized. Add the clutch set in the mix and I don't think the impact will be too bad. Some guys have stacked two flywheels weighing over 60lbs with adapters, so I'll be okay.
The main reason for pulling the adapter was to check balance on my flex plate. The adapters themselves don't really need a balance, as they are very true and closer to crank centerline. Maybe someday when I build my dynamic balancer, I'll throw in the whole thing on.
To check balance on the flex plate, I borrowed a motorcycle wheel balancer. Since the flexplate has a high diameter:length ratio, a static balance is good enough. A few of us at work played with it for a while, but the unit was very true and well balanced, so no weight was removed. We double checked our selves by adding weight at different points to verify the unit was truly balanced with the weight removed.
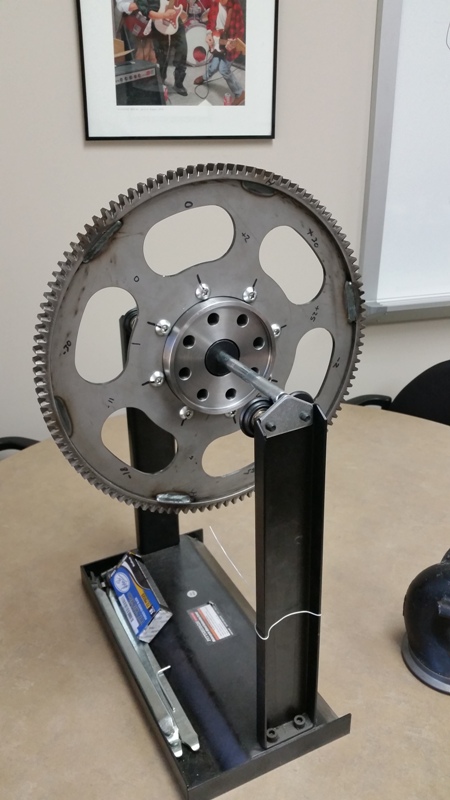